
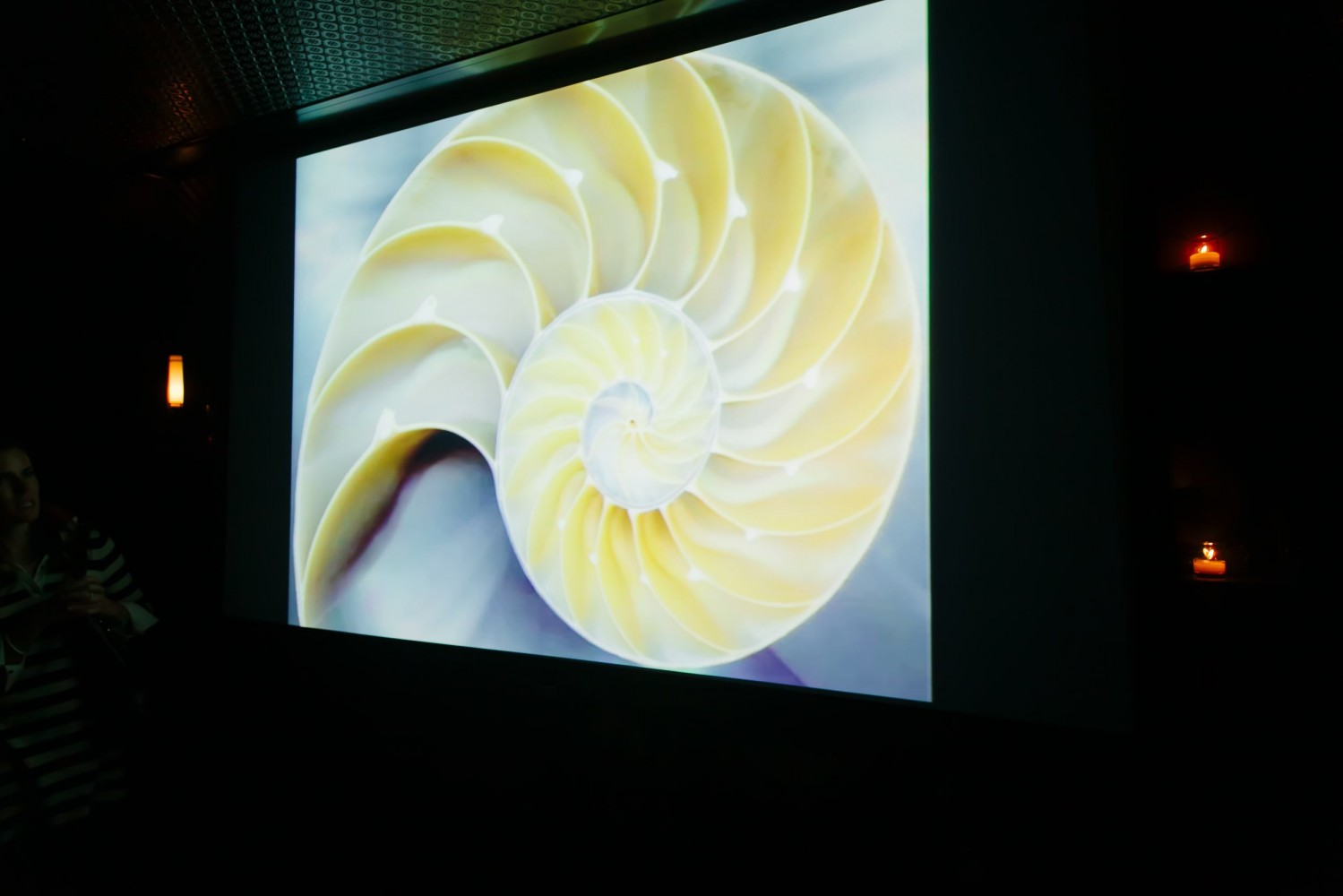
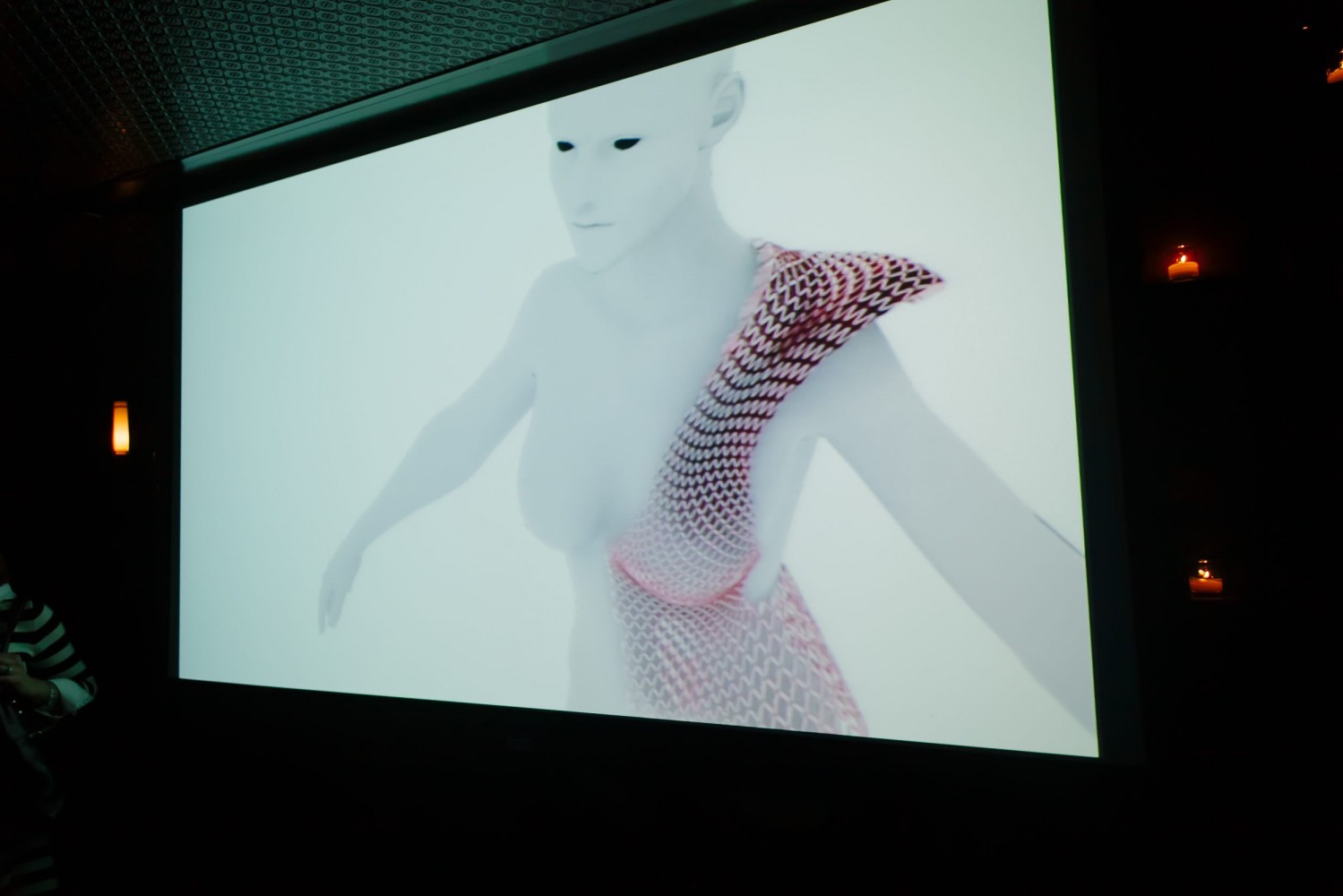
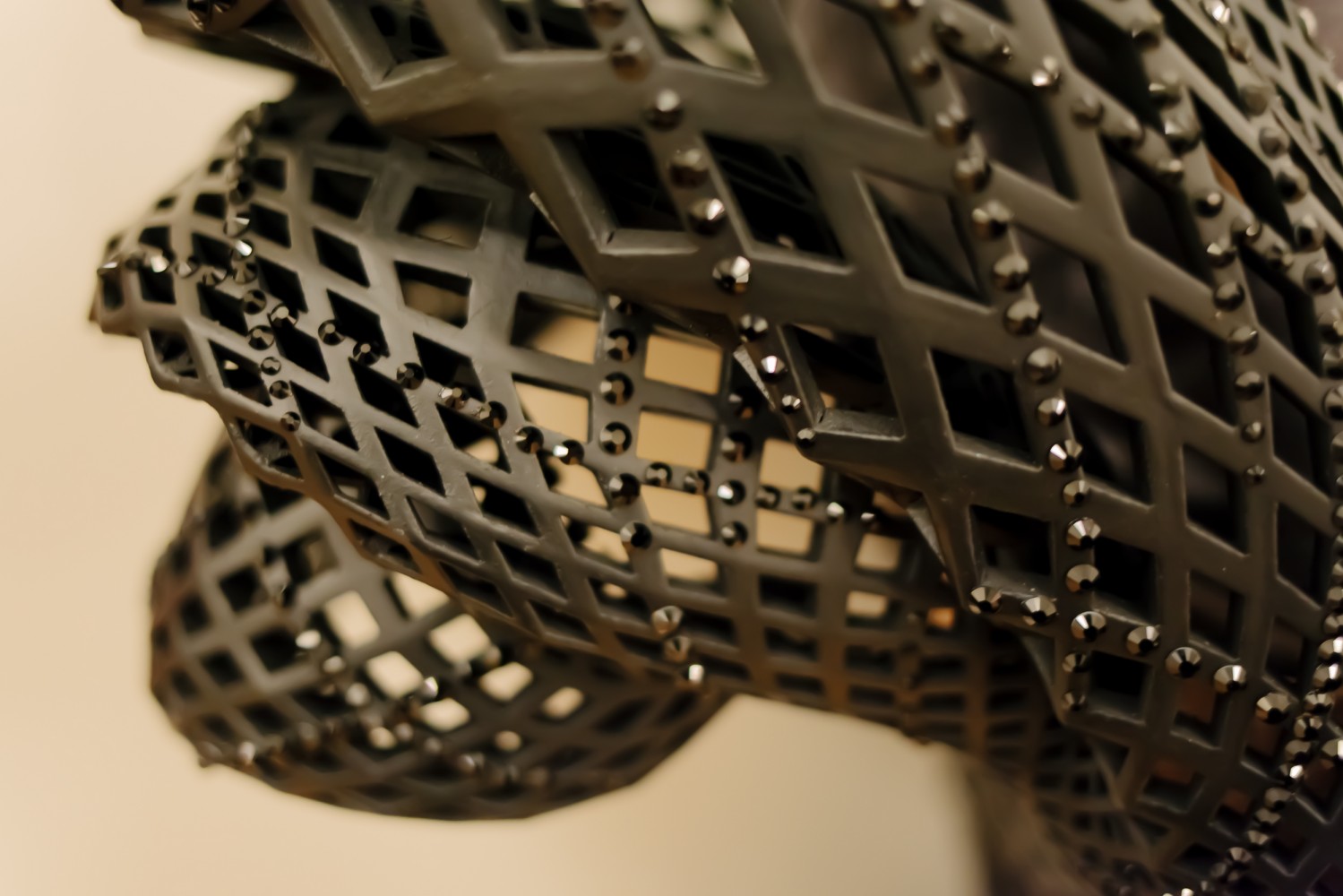
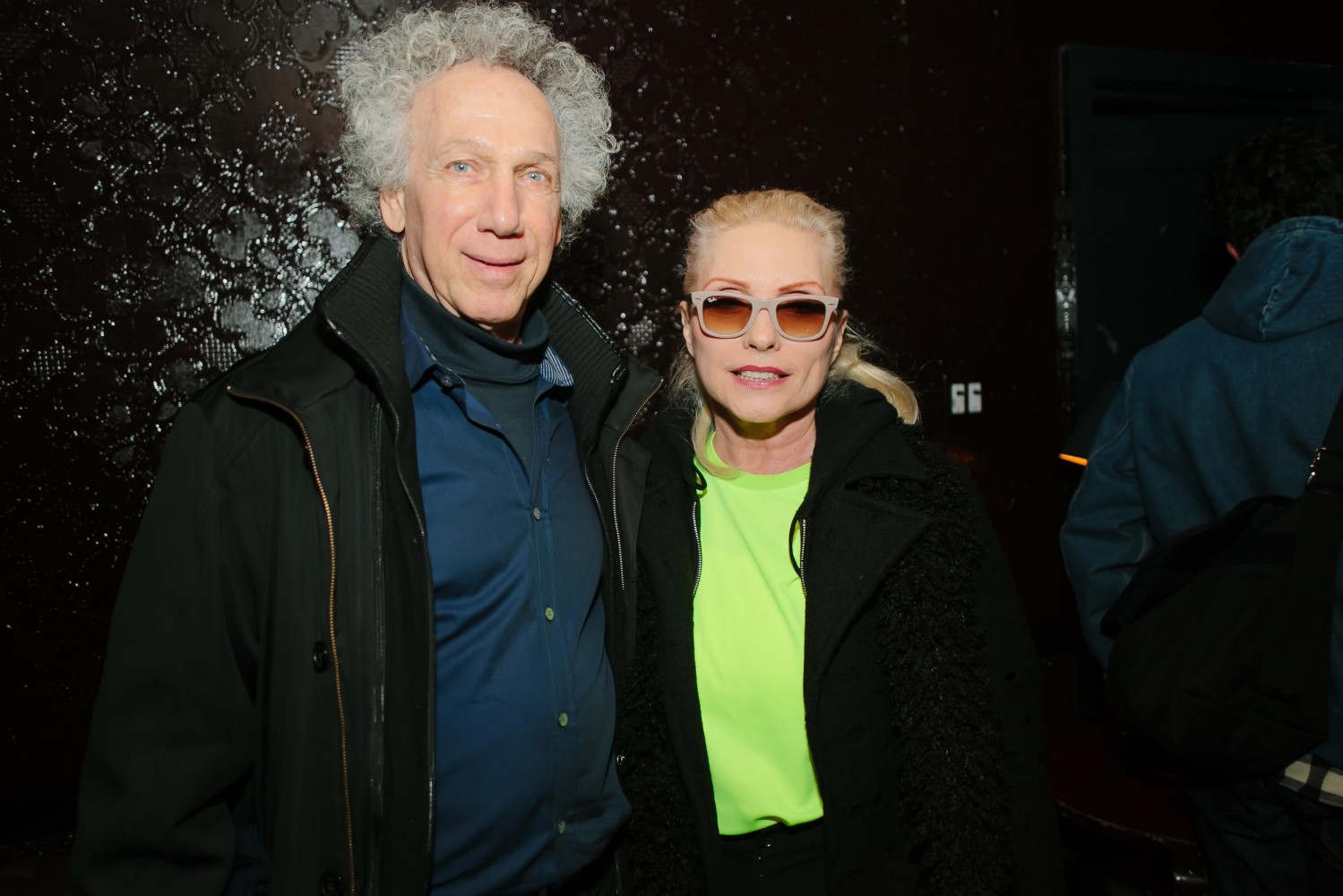
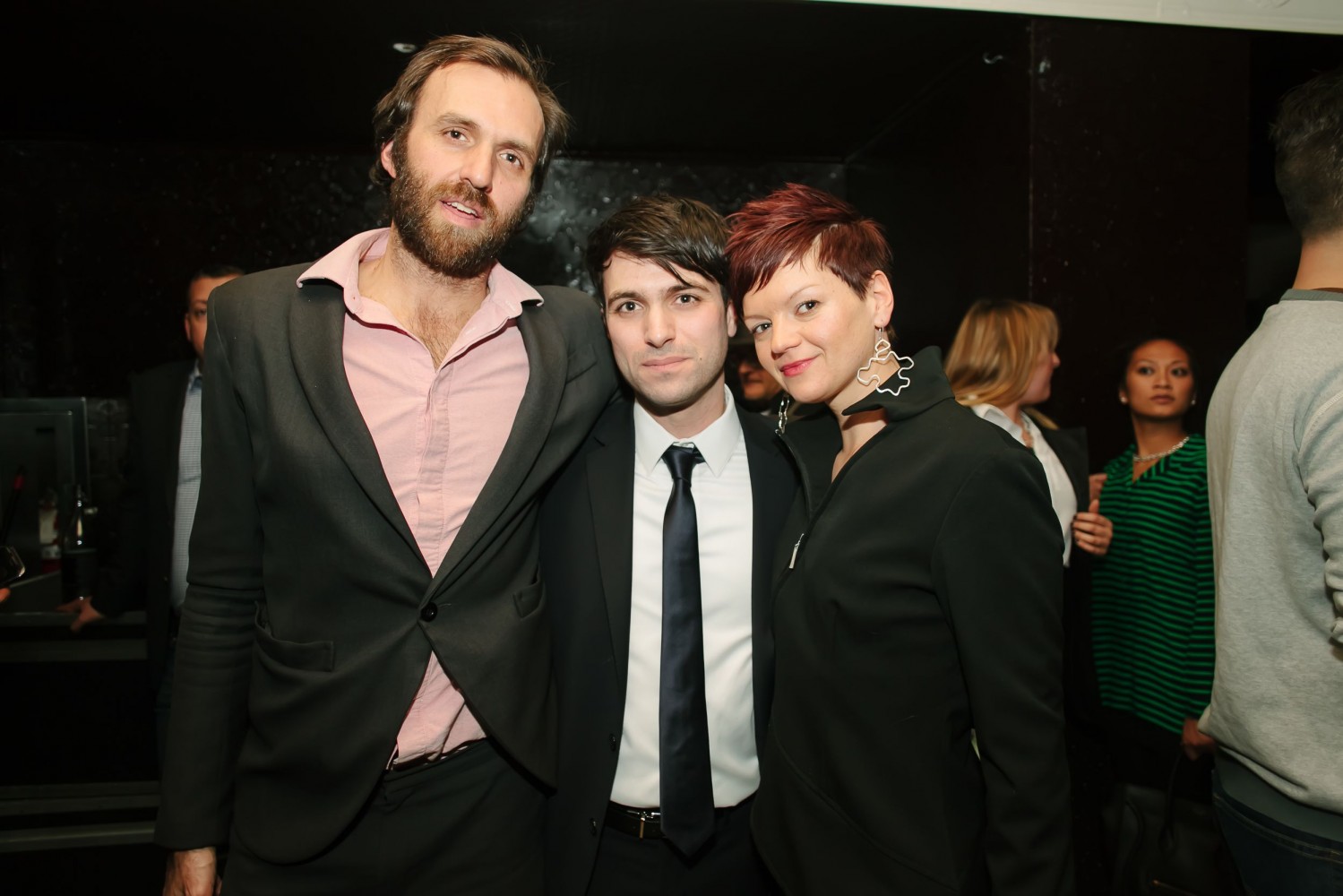
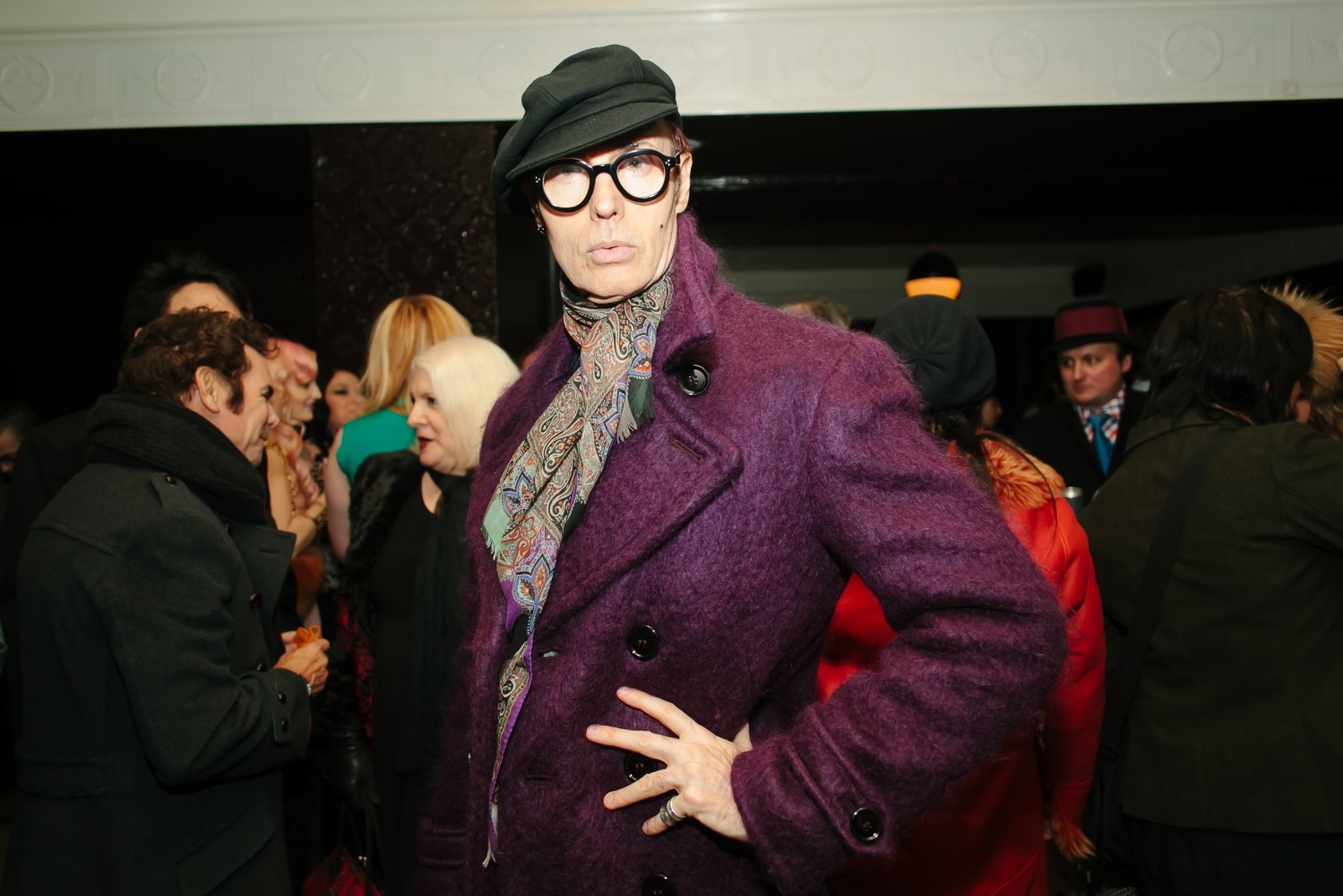
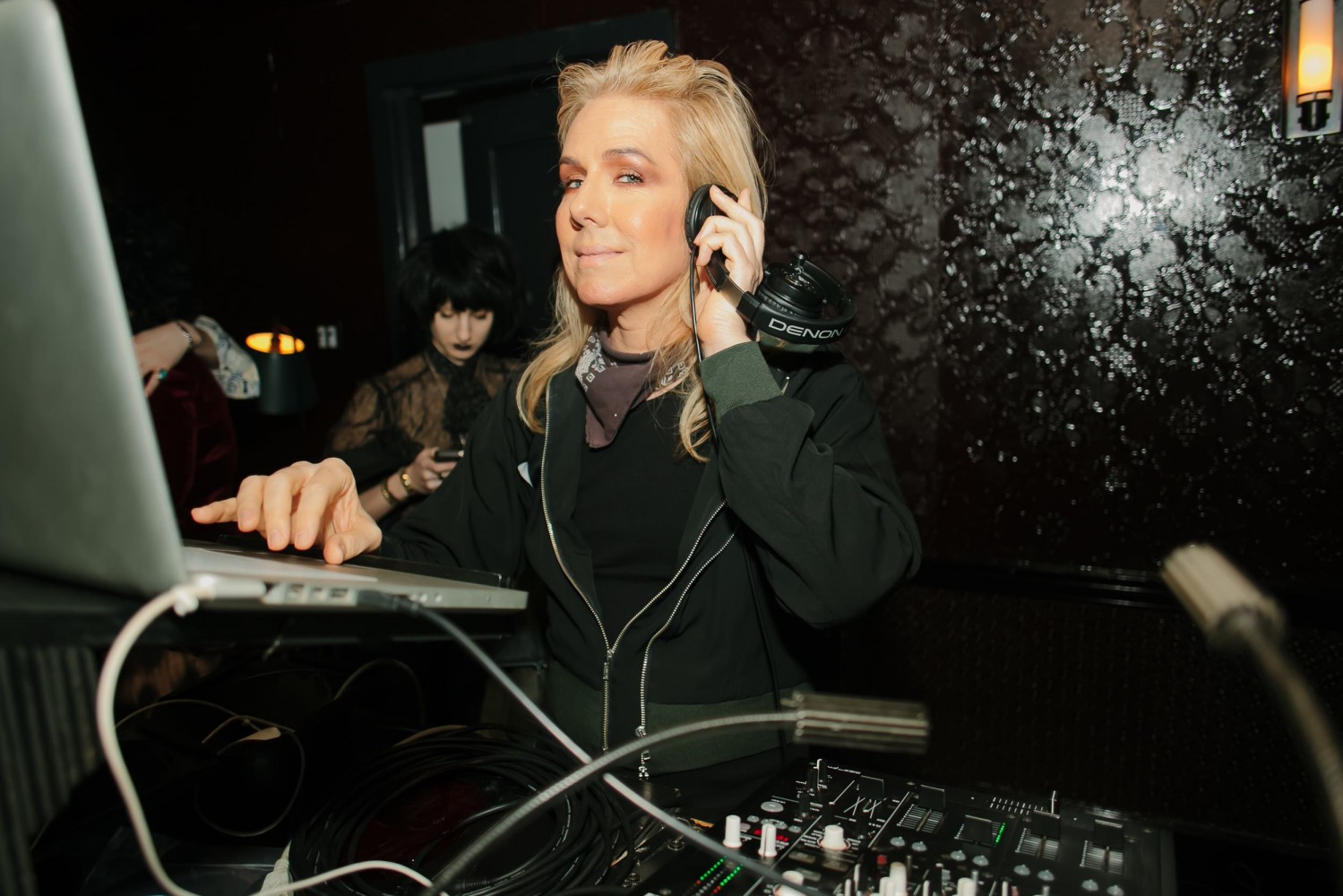
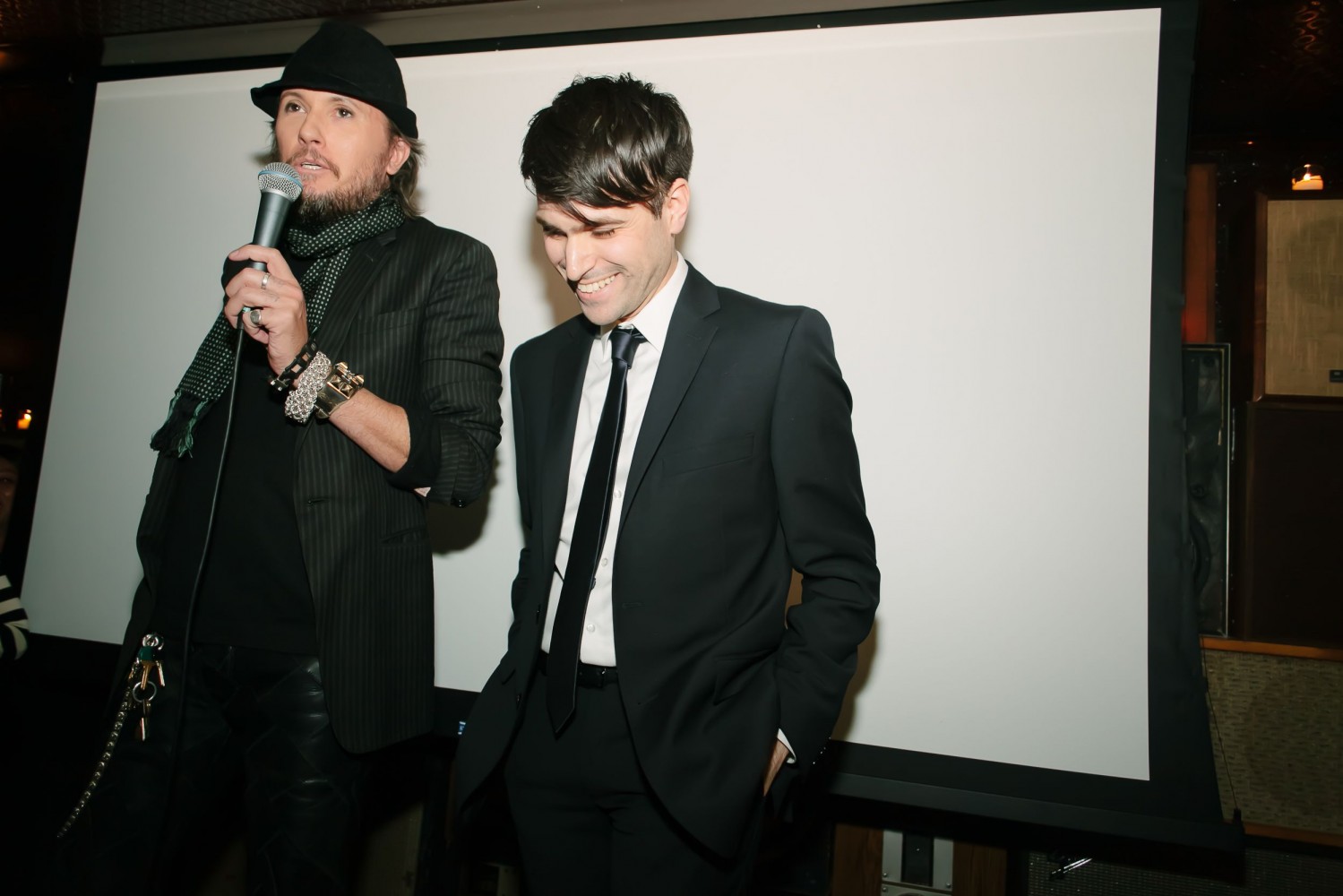
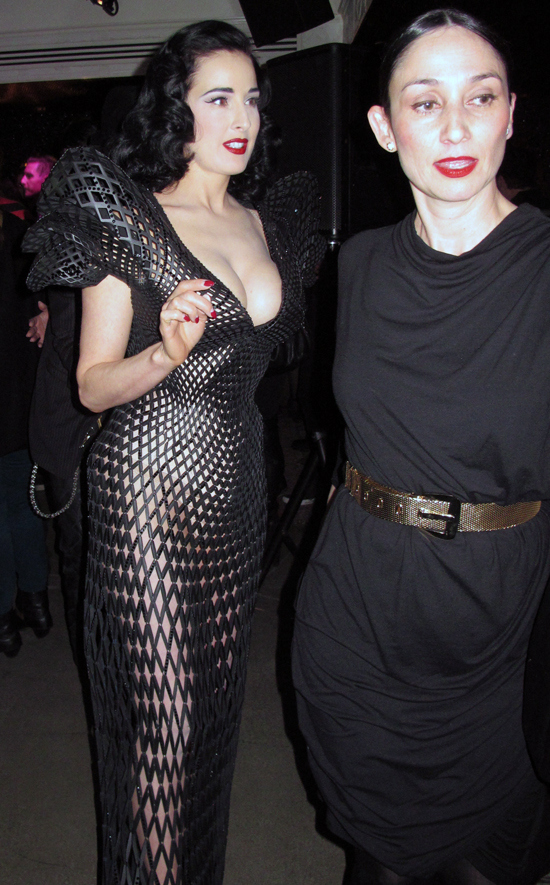
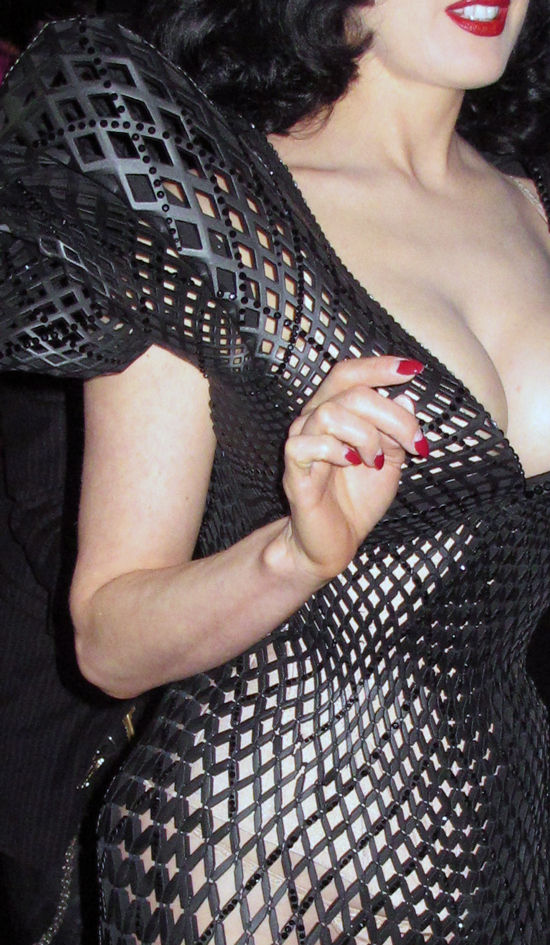
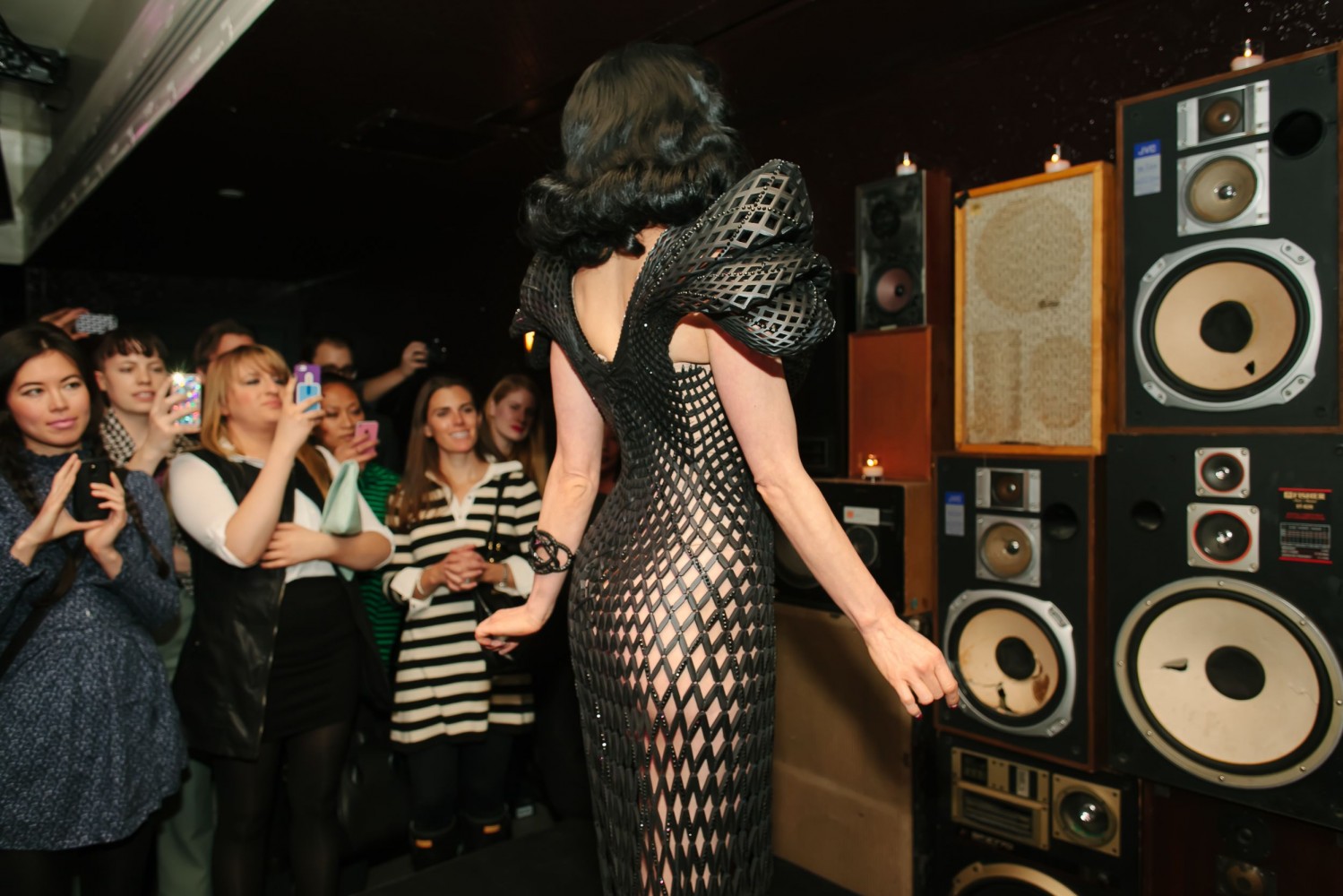
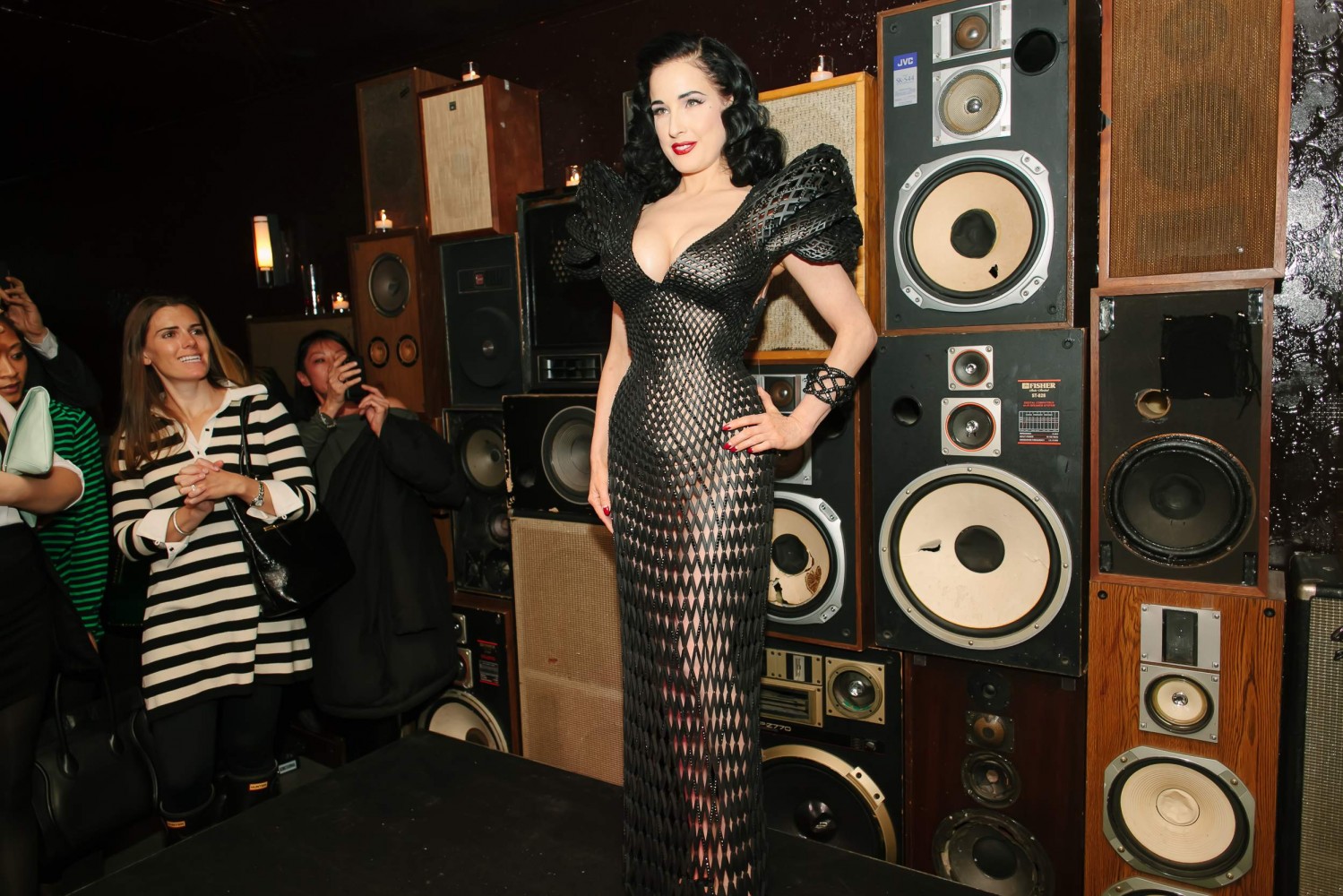
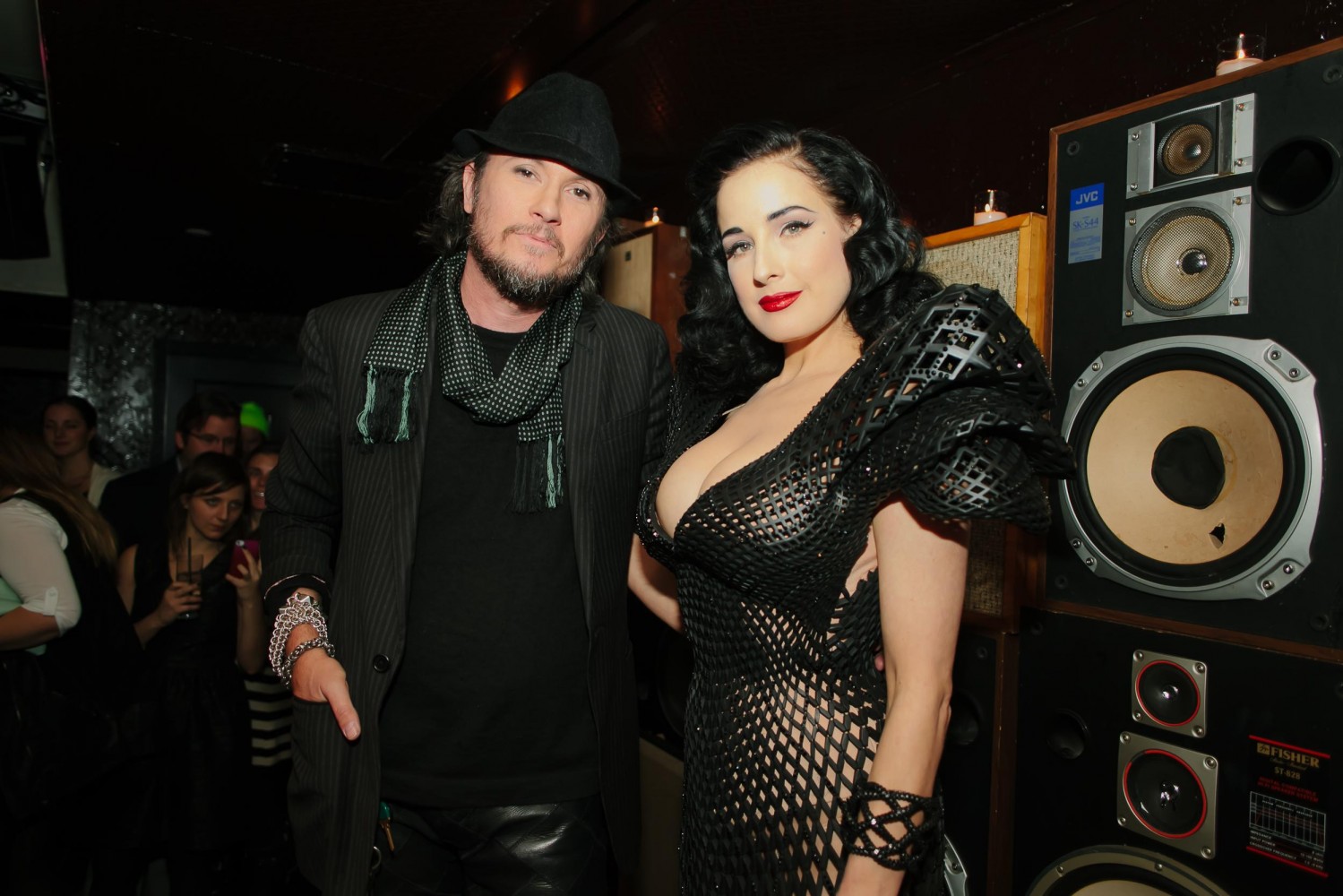
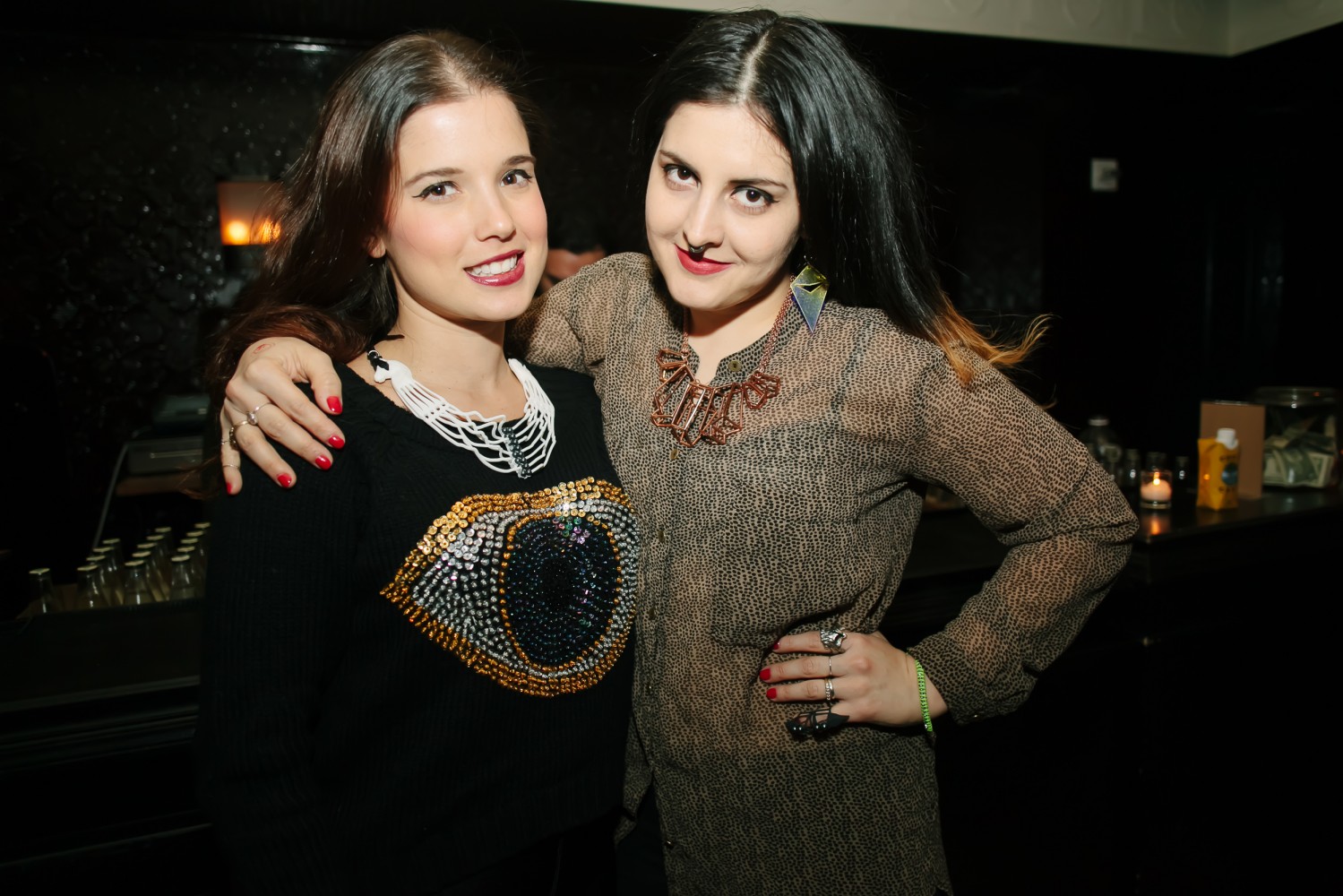
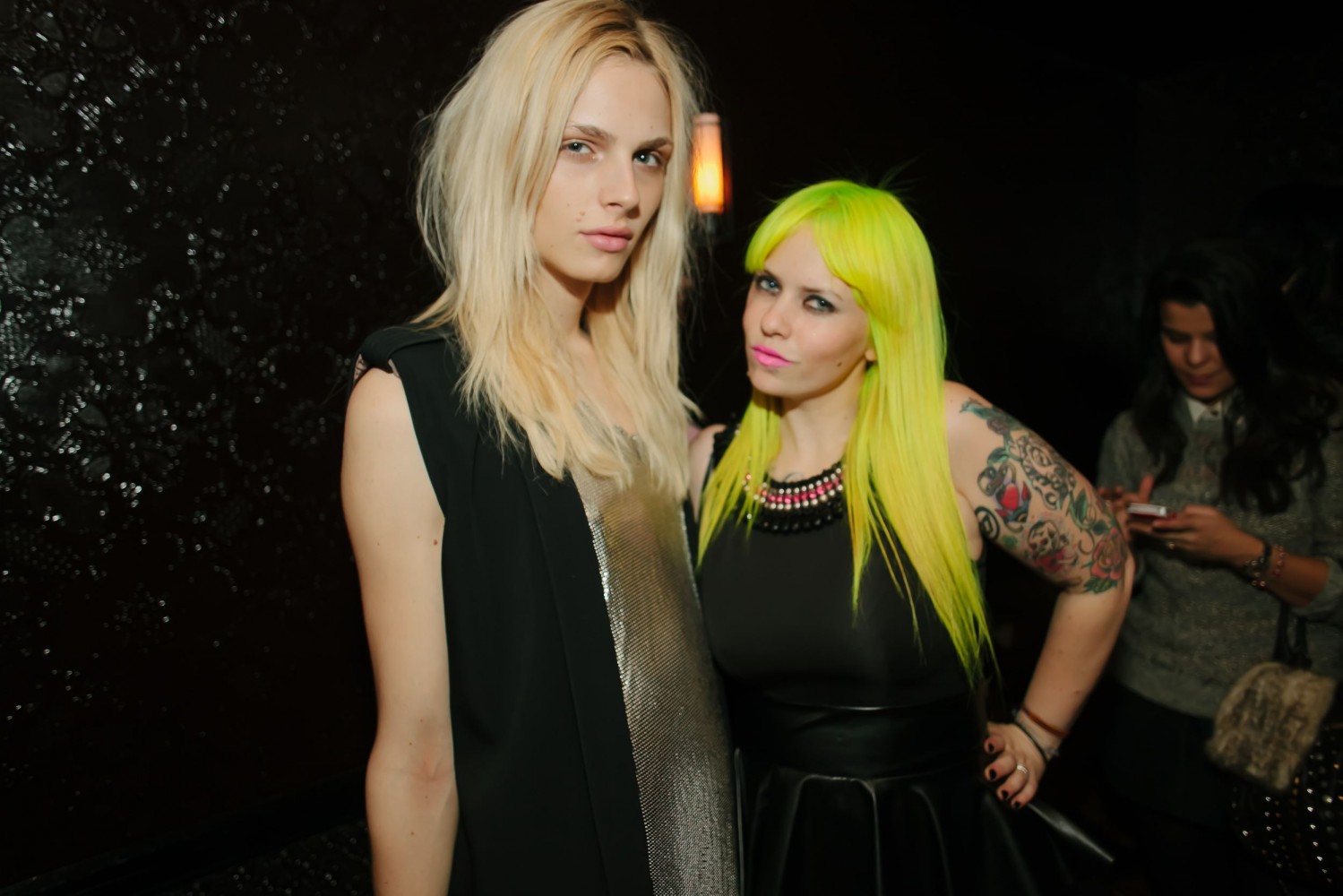
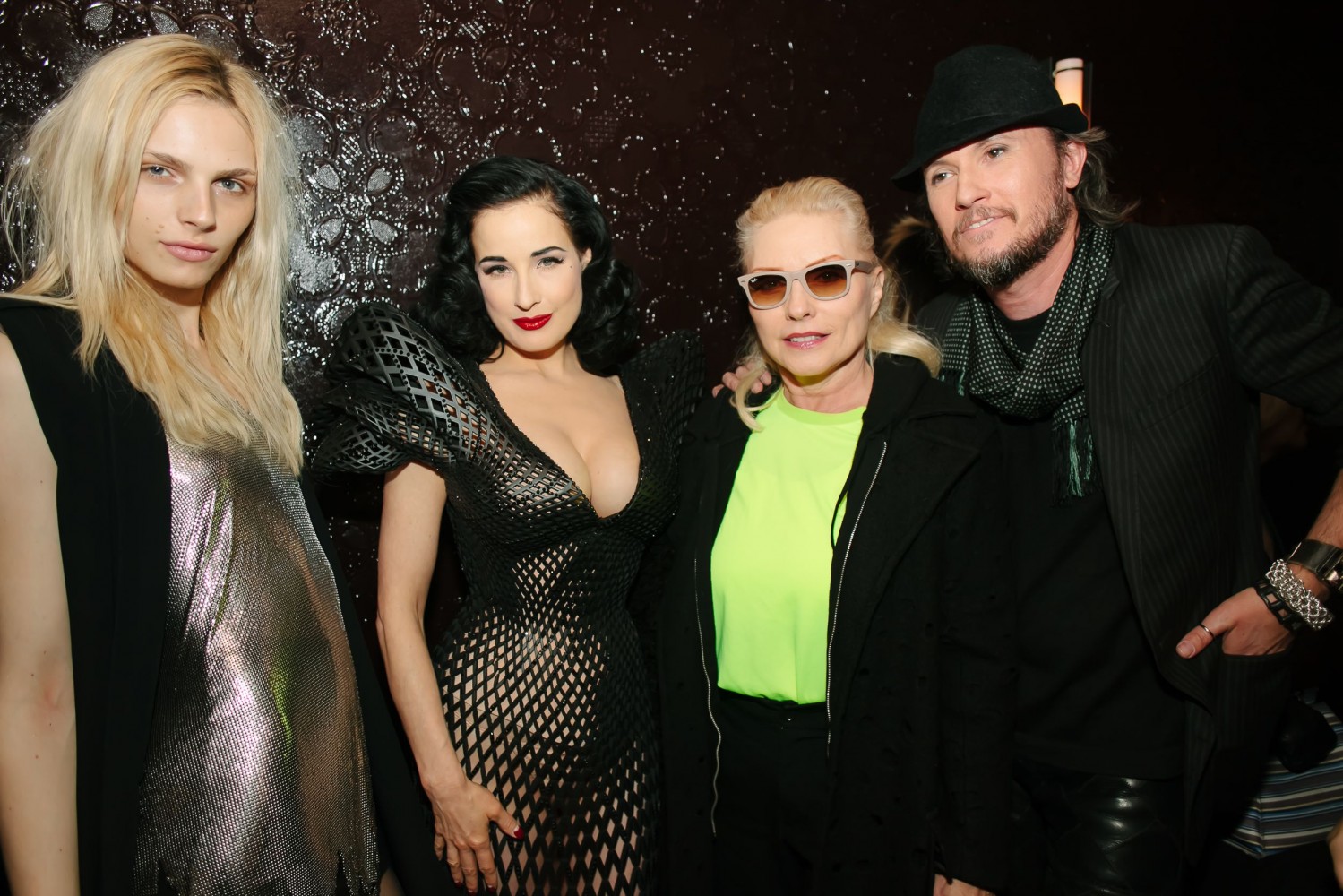
The future of fashion is here. Well, almost. The first fully articulated 3D-printed piece of fashion is now a reality. This mind-boggling work by Michael Schmidt was brought to life on stage last night at the New York outpost Ace Hotel when Dita Von Teese was laced up within an inch of her life in this high-tech haute couture.
Queens-based 3D-printing pioneers Shapeways enlisted Michael because of his incredible body, too…of work. For the last three decades Michael has sculpted, welded, cast and crystalized stunning feats of costume for a galaxy of singing superstars, among them Madonna (her last four tours), Rihanna, Gaga, Cher, Janet Jackson, Fergie and longtime friend Debbie Harry, who kindly turned out for the debut Monday night. Also there were legends of New York pop life, including deejay Miss Guy (filling Liberty Hall at the Ace with his incredible song selects), photographer Bob Gruen, deejay Billy Beyond, dandy Patrick McDonald and other dear pals of Michael, whose own imprint on life in this big city includes the infamous Squeezebox. But I digress…
Architect Francis Bitonti was teamed up with Michael, playing no small part in this process. It was one of the reasons I came to New York this week. I not only wanted to support Michael through the evening (and it was admittedly fun cranking out a press release, coordinating guests and press at the event, and overall dashing about), I also wanted to be a part of this historic evening. Clearly so did other friends such as our makeup artist pal Kathy Jeung, who stayed another day in town just to be there. The impromptu afterparty in the Breslin bar with friends in from L.A. (for this, Dita’s opening here in NYC Wednesday night and other reasons) was a late-night hoot.
For the last few months, Michael and Francis worked relentlessly to crack the nut that has so far characterized any 3D-printed fashion. Because of its inherent inflexibility, works by the likes of leaders in this arena such as Iris Van Herpin have been frozen pieces worn almost more as an accessory than a piece of clothing. Most recently, that Dutch designer rolled out pieces with motility by using rubber.
In contrast, what Michael, Francis and Shapeways achieved was actually deciphering how to engineer a piece using the powdered nylon that has long been a hallmark of architect and automobile modeling. No thread, no needles. The “textile” is actually the sintered nylon, albeit speckled with 12,000 Swarovski crystals that Michael and his team hand applied on the finished piece. His muse and model would be friend Dita Von Teese, so, of course, it would have sparkle.
“Francis was able to take my sketches for the dress, which I created specifically for Dita, and render those in the specialized language of the software,” says Michael. “The fluidity of the joints is all 3-D printed, layer upon layer of fine powdered nylon within the preheated chamber, based on information by the CAD file. The laser ‘sinters’ the nylon into form, a process known as select laser sintering, or SLS. It’s an articulated fabric built into the 3-D print itself. It’s something that’s never been done.”
Michael’s template was the Golden Ratio theory by 13th century theorist Fibonacci, whose formula for beauty continues to be applied by artists and scientists alike. At the core of the theory is that the spiral exists throughout nature, from a human ear to the pinecone to the galaxy. “It all comes down to mathematics,” he notes, “beauty realized through mathematics.”
He and Francis applied the spiral formula to the computer rendering of the dress, in a mesh that would undulate around the body in the most feminine way possible. For this reason, he tapped old friend and muse Dita Von Teese, whom he deems as the consummate classical beauty. While the shape was built over a nude silk corset, most of the architecture of the silhouette, from the voluminous shoulders to the cinched waist, is the result of the hardened nylon powder. The floor-length gown moves and expands according to Dita’s body contours because of the netting pattern.
The printer produced 17 sections that were then hand-linked together into the dress. (Much of Mr. Schmidt’s work in sterling mesh and other materials over the years involves this time-consuming process.) The 3-D printed dress was then painstakingly polished and lacquered black, and then finished in crystals.
Beautiful to look at? Yes! But it’s the technology behind it that deserves the headlines. Check out the video below to get a better understanding of it.
Unless noted, all photos by Jeff Meltz Courtesy of Ace Hotel
Posted in Craft, Current Affairs, Design, Fashion, TechnologyLeave a Comment